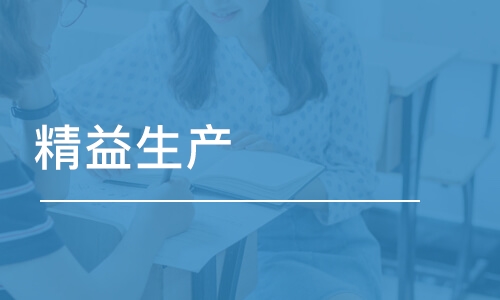
广州精益生产
课程班型小班
上课时间任意时段
课时数量请咨询
课程简介
精益化生产模式
课程背景:
本课程主要是以管理学基本理论为核心,以小批量多品种生产企业“制造效率现状”→“造成效率浪费的原因”→“提升生产效益方法”为基本课程逻辑,以精益生产思想为主线,通过大量企业生产管理案例,讲解生产现场管理在“人、机、料、法、环”各部分的管理要求及现代生产管理的基本思想;
本课程通过对生产业绩及其影响层级的层层展开剖析,循序渐进地讲解生产管理业绩提升的步骤与方法,从而避免了传统的生产管理课程将“人员、机器、工艺等要素”孤立讲授,而导致工厂管理者学习不能连贯,接收信息不成系统的问题;
管理最终是为经营业绩服务的,通过对生产业绩的直接剖析与讲授,使工厂管理者充分认识生产中4M1E的相互影响,学会系统性提升生产管理能力的方法及了解精益制造的改善思想。
课程收益:
● 形成对低成本高绩效生产管理的全面框架性概念;
● 掌握生产环节各种成本浪费的原因;
● 掌握工厂生产盈亏平衡与成本目标设置方法;
● 掌握生产绩效架构与绩效评价标准;
● 学会绩效深入分析方法与绩效推进技巧;
● 了解优化生产排产的技术,能评估并推进生产排产合理性能力提升;
● 了解物料存量的设置与管控方法,能推进工厂物料合理存量管制。
课程时间:2天,6小时/天
课程对象:生产经理、计划物流主管、车间主任
课程方式:理论教学+实操演练+案例讲解
课程大纲
第一讲:认识生产制造的效率浪费
引言:中小制造型企业的浪费首先来自工作时间上的损失,无论由于计划组织不当形成的停顿,或者设备保障不力形成的挡工,又或工艺技术落后造成的不良,最终反映于生产效率低下、制造费用超高、员工抱怨满腹、工厂管理混乱;
究其原因,工业产品市场需求已从物资稀缺转变为过度饱和,产品结构也从单一型号产品大批量需求衍生为多品种小批量需要,进而推动工业生产组织模式向柔性化、智能化制造方向进化。
大量中小制造型企业还没完成从作坊式生产向批量化制造的转型过程,就必须面对市场品种的多元化和需求的快速交付带来的巨大压力,本讲从对生产的发展演进过程梳理开始,引导到学员对生产利用率现状的剖析,明晰工厂目前的效率浪费程度。
1.生产经营模式的四次转变历程:作坊式生产→分工化生产→连续化生产→柔性化生产
2.劳动分工生产方式的作用——某企业劳动分工管理形成的低成本制造优势
3.科学化管理的核心思想——降低劳动力的疲劳程度以提升资源的利用能力
案例:流水线生产与标准化作业对劳动效率的改善
4.我们的生产利用率现状——综合利用率OEE构成
案例:企业生产综合利用率分析数据
第二讲:解析生产效率浪费的原因
引言:由于传统的工厂管理模式不能适应现阶段市场需求的转变,导致各种效率浪费被放大加剧,往往企业没有清晰认识到从优化组织方式上减少浪费提升效率,迷信或被迫于资源上的追加投资,过多的设备投入、过高的融资借贷、过量的劳动力引进和过度的工厂规模,进而背上更大的成本包袱,使其不堪重负;
本讲从工厂常见的效率浪费入手,详细剖析各种浪费的成因,引导学员正确理解工厂的经营管理困惑,明确内部效率改进的方向。
1.等待浪费现状分析
案例:企业辅助作业与主生产作业时间不匹配形成的损失
2.搬运浪费现状分析
案例:上卸货形成的料率浪费与叉车的成本浪费
3.过度加工现状分析
案例:物料批量性流转导致的质量成本浪费和让步接收损失
4.动作浪费现状分析
案例:动作经济性分析对手工包装作业的效率改善
5.不良浪费现状分析
案例:企业过程质量控制缺失形成的不良品浪费
6.库存过量浪费现状分析
案例:企业缺失远期库存变化监控导致的存量增加
7.非准时生产浪费现状分析
案例:加速物流的三大条件:产线平衡、连续物流和拉动生产
课堂研讨:钣金制造现场浪费分析研讨
第三讲:制造产能负荷能力提升
引言:产能负荷能力即:计划使用工时占可用工时的比例,反映制造资源能充分利用的程度;造成产能利用率低下常见有三大“罪魁祸首”:计划组织不合理占用过多资源;设备维护不当造成经常性停机挡工;工艺切换速度过慢导致长时间等待。低水平的产能负荷能力使工厂物不能尽其用,人不能尽其责;工厂为维持其收益水平而实施的低成本资源投入又带来了内部抱怨严重,异常问题加剧的一系列恶性循环。
本讲从生产计划组织为预留生产资源以备后续插单而控制资源使用,以信息化手段实现低成本高效率设备维护,和通过标准化作业实现同步化快速工艺切换三方面讲解提升工厂产能利用能力的思路和方法。
1.主生产计划的核心原则——制造资源的充分利用
案例:某企业主生产计划策划的流程与产销协调方法
2.设备全面维护保养的基本思想
案例:从海尔、电信售后服务中心反思如何使用信息化手段实现生产自主高效维护
3.工艺快速切换的基本方法
案例:某企业全自动机器团队快速换线的作业改善
第四讲:制造连续作业能力提升
引言:连续作业能力即:设备运作作业工时占计划排产工时的比例,反映制造现场的生产效率维持程度;瓶颈工序产能即是工厂的理论产能,只有瓶颈工序连续满负荷作业才能实现生产的连续产出;
而受制于前工序推动式生产排产导致的工序前后加工顺序不衔接,前后工序产速不一致造成的瓶颈停顿,以及物料流转批量不合理形成的瓶颈工序物料间歇供给等因素影响,使瓶颈工序无法实现连续运行,而增加了现场协调组织的工作量,加剧现场管理的混乱程度。
本讲从瓶颈工序生产拉动,产线速度平衡与连续物流转序等方面讲解提升制造连续作业能力的方法,帮助学员掌握现场生产有序控制的基本方法。
1.拉动生产的基本方法
案例:某企业推动生产排程的困惑与瓶颈拉动改善的收益
2.拉动生产的核心条件——产线平衡改善技巧
案例:某企业单元式成组布局与一个流成线布局的结合使用
第五讲:产品一次合格能力提升
引言:效率的提升绝非以牺牲质量为代价,赶产量也绝不是赶不合格品的产量。产品质量问题一般有三种现象:持续发生型问题、间歇出现型问题和突然变化型问题。区分持续发生型问题的设计源头错误的原因,区别影响间歇型问题的资源或管理变异性因素,以及查找导致突然变化型问题的失误性变化,并加以改善和控制,使从源头上保障产品质量一次合格能力提升的关键。
本讲围绕如何区分制造过程资源或管理性变异因素,以及如何防范生产失误两方面讲解零缺陷质量的实用控制手法,提升学员对有效控制产品质量的系统方法的掌握
1.失误性问题的六大原因与防错方法
案例:生产过程中实现员工岗上技能教练的方法
2.组间与组内变差型号对从资源方向或管理方向实施一致性质量改进的判断
案例:从打靶弹痕判断质量变异根源的方法
3.质量控制的改善逻辑——技术优化降低损失、质量防错杜绝原因、优化控制提升效果
案例:企业技术质量策划全过程推进流程
第六讲:标准化作业能力提升
引言:标准化作业控制的目的是优化作业过程,提升人、机匹配程度,在减少人、机间相互等待时间的同时减轻员工劳动强度,进而提高员工作业能力和工厂产出效率;。这与传统制造现场罗列操作步骤、堆砌质量要求的作业指导书不可同日而语。
同时,只有劳动方法标准化进而才能实现员工训练科学化,使“生手”快地通过岗前、岗上训练转变为“熟手”,这是科学管理原理的核心思想之一。而传统工厂在标准化作业控制方面基本处于放纵自发状态,从未识别和设计员工合理的作业过程,从未优化和规范员工高效的作业动作,依靠粗放的师徒制管理模式提高员工技能;使企业生、熟手效率差异巨大,学徒成长缓慢,新工大量流水,用工成本上升等一系列问题滋生。
本讲以加工、搬运、维护等各种常见的作业活动为中心,通过大量的标准作业改善案例向学员讲解优化作业的步骤和方法,使学员掌握标准化作业的核心要求并明确自身改善点和实施方法。
1.标准化作业与多技能员工培养
案例:某企业标准化作业对降低用工条件,实现批量招生上岗的帮助
2.加工过程标准化作业
案例:某企业优化作业顺序实现效率提升
3.搬运过程标准化作业
案例:某企业物料搬运同步化作业流程改善
4.快速换模的标准化作业
案例:某企业快速换模标准化作业改善
5.设备维护标准化作业
案例:某企业全面设备维护保养标准化作业范例
课后作业:
1.学员企业瓶颈工序生产综合利用率调查分析;
2.学员企业精益化生产水平诊断自评;
3.学员企业精益化生产改善合理化建议。
精益生产管理导入实务
课程背景:
沈老师带着咨询团队走过了近300家各类型企事业单位,发现他们并不缺管理人员甚至管理精英,也不缺流程及制度,但通过深入调研及分析,发现很多单位存在以下共性:
天天加班>工资不高
计划不少>交付不了
口号遍布>执行不多
天天精益>浪费不少
说话声大>业绩声小
会议很多>问题依旧
排产靠经验>产销失衡
现场混杂盲>方法缺失
执行无标准>空谈执行
管理无体系>系统缺失
岗位无通道>人心散漫
目标无分解>停留口号
绩效无系统>只走形式
团队无活力>机制缺失
缺精细、缺方法、缺工具、缺机制、缺目标、缺绩效=缺精益管理……..
以上问题是管理人员错了吗?好像也不是,因为不可能全员错误,那问题出在哪呢?
管理系统或控制系统存在问题,管理系统无法让全员为企业的最终价值(产品或服务)实现为核心进行工作或全员缺少对整个管理系统从接单到出货一系列流程控制点的整体了解和掌握,导致了工作中冲突不断,各自为政,企业处於低效状态,影响了企业效益。
解决以上问题,让全员具有大系统精益思维方式,在大局为重的思维下进行团队协作,企业效益才能不断提升,在激烈竞争中立於不败之地。
适合对象:
总经理、高管团队、人力资源系统、生产管理系统、工程及技术管理系统、品质管理、生产计划全员、其他部门主管级以上管理人员
课程收益:
直面管理系统实质问题,并从现场咨询角度系统给出答案;
能帮企业找出不知不觉中造成巨大浪费与损耗的根本原因;
帮助企业找出杜绝这些浪费与损耗有效的根本对策;
理解富士康生产系统精髓的理论知识;
通过方法和工具、结合案例讲述,使企业管理干部具备应用各项管理提升机制;
能帮企业找出管理方式,打造高效的信息流;
打造企业高效物资流,使我们的计划不再落空;
通过软手段,完善整个管理执行系统的管理,保质保量达成客户需求;
通地硬手段,提高运作效率,保障交付和业绩。
课程大纲:
第一讲 破冰分享:生产制造业企业管理透析!
1.优秀制造企业的表现(外在表现,内在透析,怎么做到的?)
2.企业效益的三大来源及生产企业的三大流(信息流、物资流、工艺流)
3.生产企业构成的5大基本要素诠释及关系(4M1E)
4.生产制造业网状结构图
5.绩效提升的根本是什么?
6.企业机制平台诠释
7.企业文化的诠释
8.如何看待企业管理问题..?
【富士康 & 海尔-管理优点分享】
第二讲 制造工厂管理基础
1.工厂的发展史
2.精益生产发展史
3.企业管理架构
4.精益价值流
5.企业管理的六大基础:
a)沟通机制
b)权责利匹配
c)标准化体系
d)他律自律
e)改善创新
f)F).学习型组织
6.工厂管理的四大要素
a)工厂流程管理
b)工厂人员管理
c)工厂物料及供应链管理
d)工厂效率管理
第三讲 工厂流程管理
1.流程概述:工厂主要管理模块
a)人力资源管理流程
b)产品设计及开发流程
c)生产计划及物料控制流程(PMC)
d)工艺及标准化作业管理流程(PIE)
e)物料及供应链管理流程
f)品质管理流程
g)生产管理流程
h)设备设施管理流程
2.人力资源管理流程
a)工厂人员组织架构及编制
b)全员薪酬体系
c)员工绩效管理
d)雇员职业发展与规划
e)企业文化建立及宣导
【工具引用--《岗位说明书》】
【工具引用--《企业培训计划》】
【工具引用--《薪酬结构案例》】
3.产品设计开发流程
a)产品及产品编码标准化
b)零部件及图纸标准化
c)物料清单及其完整性(BOM)
d)物料编码标准化
e)产品开发过程中的验证、审核、批准程序
【工具引用--《物料清单BOM》】
【工具应用--《产品工艺卡》】
4.生产计划与物理控制流程
a)如何合理制定生产计划
b)物料需求计划制定
c)物料需求计划与库存管理
d)生产计划管理
e)衡量PMC流程管理的绩效指标
【工具引用--《MPS主生产计划(月度)》】
【工具引用--《三日滚动计划》】
【工具引用--《物料需求计划》】
【工具引用--《发货计划》】
【工具引用--《盘点表》】
5.工艺及标准化作业流程
a)产品制造工艺分析及制定(PE)
b)生产作业标准化研究
c)生产线效率研究
【工具引用--标准作业程序SOP】
【工具引用--标准工时UPH】
【工具应用--工艺路线图】
6.品质管理流程
a)QA质量体系的建立与维护
b)客户标准与工厂标准之间的转化
c)QE的职能与定位
d)QC的职能与定位(IQC\IPQC\FQC\OQC)
e)供应商品质管理
f)供应商品质管理与SQE
g)衡量品质管理流程的绩效指标
【工具引用--QC工程图】
【工具引用--标准检验规范SIP】
【工具引用--单点课程OPL】
第四讲 人员管理
1.一线员工管理四原则
2.新员工&三新员工影响分析
3.生产线员工培训(入职培训与在线培训)
4.一线干部-班组长角色定位及职责定位
a)班级长角色定位
b)班组长的基本职责
c)班组长的三大权力
d)班组长必备的四种本领
e)班组长五项使命和九角色
【工具引用--班组长晋升通道与五年职业规划】
【工具引用--生产系统岗位职责展示】
5.造成管理人员效率低下的四大因素--部门职能交叉、岗位职责不清晰、分工不明确
【案例 现场问题焦点之权责划分】
6.造成管理人员效率低下的四大因素--无详细工作分析、职员在低负荷下工作
【案例 现场问题焦点之岗位工作分析表】
7.造成管理人员效率低下的四大因素--职员缺乏培训、不熟悉部门及公司运作程序
a)管理人员培训--入职培训
b)管理人员培训--部门见习
8.造成管理人员效率低下的四大因素--缺乏管理方法与管理工具
a)“泰勒--科学管理;戴明--全面质量管理;德鲁克--目标管理”三大管理思维的逻辑关系!!
b)“敏捷生产 & 精益生产”的关系!!
第五讲 精益供应链
1.供应链的重要性及普遍性问题(或客户现场问题及对公司制造系统产生的影响)
2.生产计划制定
【工具引用--主生产计划->滚动计划->数据看板->异常处理->案例分析】
3.物料控制
a)MPS与MRP
b)采购交付控制 & 物料到达状况
c)物料库存控制
d)衡量物料控制的绩效指标
【工具引用--物料标识卡】
【工具引用--盘点管理流程】
【工具引用--物料需求计划】
4.采购管理
5.供应商管理(选择、评审、考核)
6.物料管理
【工具引用--生产领料单】
【工具引用--生产补料单】
【案例 降低物料成本分析】
第六讲 生产现场管理
1.生产现场管理
2.周生产计划平衡
3.生产线产能确定方法
4.生产线数据采集
5.全员生产效率
6.停线时间分析
7.停线原因分析
8.效率的定义
a)真效率与假效率
b)个别效率与整体效率
c)瓶颈与短板管理
d)浪费意识和价值意识
9.八大浪费与改善
a)不良品浪费
b)过量生产浪费
c)过剩浪费
d)动作浪费
e)库存浪费
f)搬运浪费
g)等待浪费
h)管理浪费
10.现场5S管理
a)三定
b)推行技巧--八大要诀
【工具引用--《班组早会流程》】
【工具引用--《班组交接班记录表》】
【工具引用--《异常处理流程》 &《异常快速处理单》】
【工具引用--拉动式看板《数据管理看板》】
【工具引用--《生产日报表》】
【工具引用--《生产实绩分析表》】
【工具引用--《工作日志(班组长)》】
【工具引用--《开班点检表》】
【工具引用--《5S稽查表》】
【工具引用--《安全隐患排查表》】
【工具引用--《稽核日计划》&《整改通知单》&《稽核战报》】
【工具引用--《生产领料单》&《生产补料单》】
【工具引用--《三日滚动计划表》&《生产指令单》】
【工具引用--《设备保养计划(年度)》&《设备点检表》】
【工具引用--《范例 标准作业程序SOP》】
【工具引用--《范例 标准检验规范SIP》】
【工具引用--《范例 单点课程OPL》】
第七讲 精益生产推行--“六大方法”和“六大工具”
1.六大方法:
a)三要素法:标准+制约+责任
b)分段控制法
c)限制选择法
d)稽核控制法
e)数据流动法
f)横向控制法
【工具引用--《范例 数据流动法》&《范例 管理控制卡》】
【工具引用--《范例 基于三要素法则的流程设计》】
2.六大工具:
a)六日工作法【案例 六日工作法的应用】
b)文控体系
c)管理控制卡【案例 管理控制卡的应用案例】
d)数据看板【案例 数据看板的应用案例】
e)异常快速处理与案例分析【案例 异常快速处理的应用案例】
f)数据绩效考核【案例 数据绩效考核的应用案例】
第八讲 管理方法落地思维 & 课程总结
1.革除执行的四大陋习
2.管理的五个DING
3.课程总结
4.培训跟进
精益生产管理落地路径与实践特训班
【课程背景】:
“精益”概念的提出虽然缘起于精益生产方式,但是通过近30年的发展与变革,精益生产管理早已经被世界级管理水平的企业不断改进和提升,早已经从生产制造层面拓展到整个企业层面,并且精益思想成为了企业的核心价值观。
企业运作的目标是通过持续的消除浪费并向客户提供完美的价值,从而实现企业的内部增值过程。本课程提供了精益系统整体方案,为你介绍起始于丰田汽车公司的精益思想和精益改善系统的实施过程。目的在于:从客户的角度出发,认识价值和发现过程中的浪费,并持续消除浪费;采用精益化的拉动系统,有效控制过程中的库存,降低制造周期时间,提高过程的效率(库存、资金的周转率)及客户满意率;为降低或消除过程中的非增值活动,通过降低设置时间、目视管理、瓶颈改善、均衡化生产、质量管理与变化点管理,标准化作业等具体的改善方法,降低成本并支持拉动系统的实施。
【培训目标】:
课程系统讲授了精益改善模式主要内容、模式实现基本方法、企业推行方式等技能,并针对国内企业实践中的重点、难点问题,提出了有针对性的解决方案,旨在为国内企业提供一套先进的管理模式,全面提升企业的竞争力,最终实现企业价值和利润的提升。
【课程时间】:2天/12H(6H/天)
【培训对象】:企业中高层管理人员
【培训大纲】:
第一讲、精益思想基因解码
一、TPS发展史的启示
1.精益发展历程
2.丰田如何精益
3.精益成本之说
二、LP精益制造模型
1.精益生产思想
2.精益生产模型
3.精益两大支柱
三、JIT方式实施全图
1.拉动能及时化
2.*IT系统展开
3.实施JIT三术
案例:稻盛和夫的六项精进
第二章、精益生产管理落地路径与实践:生产七大浪费改善策略
一、消除浪费产生价值
1.两大主题关联
2.重新定义三率
3.消除浪费两面
二、现场七大浪费详解
1.库存的浪费
2.等待的浪费
3.不良的浪费
4.过度的浪费
5.过多与过早的浪费
6.动作浪费的浪费
7.搬运的浪费
三、管理多种浪费分析
1.工作“等待”的浪费
2.“低效”的浪费
3.管理无 “理”可依
讨论:库存是万恶之源吗?
第三章、制定精益生产改善方向:专项从价值流着手
一、价值流工具概述
1.什么是价值流?
2.绘制价值流图十步骤
练习:现场绘制价值流图
二、价值流当前状态图
1.选择要分析的产品并手工绘制当前状态图
2.组成一个工作小组并明确职责
3.选择要研究的产品族
4.了解客户需求
5.画出工艺流程图
6.画出物流
7.画出信息流
(提示: 画产品当前状态图时建议首先用铅笔在白纸上绘制,不要试图直接用VSM的工具图绘制。那样可能会遗漏一些重要信息。)
8.定义并收集相关数据
9.绘制当前价值流图
10.在当前状态图基础上绘制价值流图
11.计算产品生产周期及增值比
12.按照前述浪费的定义,找出当前价值流图中的各种浪费,为未来价值流图作准备
案例:某产品当前价值流图绘制实例
三、价值流未来状态图
1.改善的目标是:更智慧的工作,而不是更累!
2.画出未来状态
3.计算TAKT time
4.客户lead time的目标值时多少?
5.何处可以使用连续流生产?
6.何处使用超市?
7.平衡过的生产速度和TaktTime(节拍时间)相吻合吗?
8.你如何平衡生产?
9.何处调节需求变量?
10.需要什么样的过程改善?
11.未来状态
12.未来状态消除了浪费的根本原因吗?
13.实现未来状态
14.练习:画出你所熟悉的产品价值流分析图
第四章、精益生产管理落增效改善路径:瓶颈改善
一、什么是瓶颈管理?
二、瓶颈管理的核心理念是什么?
三、瓶颈管理的实用方法‧ ‧ ‧
四、瓶颈管理怎么用?
五、结论
第五章、精益生产管理落地路径与目标——均衡化生产
一、起步
二、使生产系统的能力和需求相匹配
三、创建“定拍工序”
四、控制上游生产
五、扩大均衡拉动系统
六、保持成果持续改进
案例:均衡化生产改善案例
精益生产十大工具
【课程背景】
精益生产(LeanProduction,简称LP)是因为日本汽车业本世纪在世界崛起,美国麻省理工学院根据其在“国际汽车项目”研究中,基于对日本丰田生产方式(Toyota Production System)的研究与总结,以及对美国汽车工业的反思与总结,提出的一种生产管理方法。
“欧美企业将三分之二的研究发展经费,花在新产品研发上面,将另外三分之一的钱用在生产过程的改善;可是日本的做法刚好相反。而我认为欧美的做法是错误的,以前,发明、开发新产品是企业竞争中最重要的武器,但是现在竞赛的重心是在于生产过程的改善。”
——美国麻省理工学院管理学院院长梭罗教授。
【授课对象】生产总经理、副总经理、生产总监/厂长,供应链总监、精益/生产经理、物流经理
【课程价值】
1、明确企业经营的三种理念与精益思想的五大原则
2、掌握企业常见的七大浪费与浪费产生的原因
3、掌握价值流现状图绘制的六步骤与现状图问题的分析与改善手法
4、掌握5S三大层级,各”S”推进的要领,目视化管理的两大原则,三级水平与五大方法
5、掌握标准作业的三条件,三要素与标准作业作业的四大步骤
6、掌握设备管理的三大核心指标与自主保全的七步骤
7、掌握快速切换的七步骤与法则
8、掌握品质管理的“三不”策略与防错的十大原理
9、掌握看板运作的三种方式与看板运作的六大纪律
10.掌握问题三种类型与问题解决的八步法
11.掌握现场定位与持续改善的核心
【工具/表单】
物流布局图 / 生产计划流程图 / 浪费地图 / 价值流程图 / “三不“模型
浪费识别表 / 物料清单表 / 标准作业表 / 多能工表 / 员工技能表
【课程特色】45%理论+35%案例讲解+15%现场演练+5%点评总结
【课程时长】3-4天/16-24H
【课纲内容】
理念篇:
第一讲:精益生产概论
视频案例分析:从国庆阅兵看精益生产
一、精益生产发展的历史
二、企业永续经营的根本
三、企业经营的三种理念
四、精益生产的五大原则
五、价值—价值流—流动—拉动—尽善尽美
案例分析:多伊尔.威尔逊案例
六、企业常见的七大浪费
视频案例:烤面包
课堂演练:寻找浪费
工具篇:
第二讲:价值流程图
一、价值流图分析
1、何为价值流
2、价值流图的作用
3、价值流图分析步骤
4、价值流图解析
二、价值流现状图绘制步骤与分析
1、确定产品系列为价值流分析对象
2、产品分簇矩阵图
3、现状图绘制步骤
4、现状图分析改善
案例分析:某企业价值流绘制与分析
三、绘制未来图
1、选定节拍时间
2、确定收货方式
3、确定何处引入连续流
4、确定何处引入拉动系统
案例分析:某企业价值流未来图分析
第三讲:现场5S与目视化管理
一、为什么要做5S
视频案例:裸男在家
二、5S的三大层级
三、各“S”推进要点
1、“整理“推进要点
2、“整顿”推进要点
3、“清扫”推进要点
4、“清洁”推进要点
5、“素养”推进要点
视频案例分析:历史转折中的片段
四、目视化概论
1、目视化定义
2、目视化三要素
3、目视化两大原则
4、目视化三级水平
五、目视化常用工具
1、视觉类工具
2、听觉类工具
3、其它表现形式
案例分析:某日资企业现场目视化案例
第四讲:标准化作业
一、标准作业与作业标准的区别
二、标准作业的三条件与三要素
三、标准作业的作成步骤
现场演练:标准作业票作成
四、实施标准作业改善的步骤
1、改善的步骤
2、如何从标准作业“三件套”找问题
3、运用动作经济原则改善
第五讲:全员生产性保全TPM
一、设备效率的三大指标
二、设备效率之OEE提升
案例演练:OEE计算
案例分享:某企业OEE效率提升案例
三、自主保全活动展开
1、开展自主保全七步骤的思考方式
2、自主保全活动七步骤
3、成功开展TPM自主保全的12关键点
4、成功开展自主保全所要解决的问题
案例分享:某台资自行车集团自主保全
第六讲:快速切换
一、为什么要实施快速切换
视频案例分析:F1换轮胎
案例讨论:快速切换对生产周期有什么影响
二、快速切换分析
三、减少切换的改善顺序
1、准备更换损失时间的实际状况调查
2、高层领导的态度表明和项目组的组成
3、现场观察和连续稼动分析
4、把切换结果整理为三种浪费分析
5、全员参与的改善实施计划制定
6、改善实施,评价与推广
四、实现快速换模的七步法
案例分享:某日企注塑模具切换案例
五、快速切换法则
第七讲:防错
一、精益生产两大支柱
二、品质管理“三不”策略
1、技术面
2、作业面
3、管理面
三、防错/防呆
1、失误与缺陷
2、防错的四个等级
3、防错/防呆十大原理
4、防错装置
案例分析:某企业防错案例
第八讲:看板管理
一、传统生产方式与JIT方式的比较
二、几种常见的准时化生产方式
1、顺序拉动系统
2、后工序拉动系统
1、混合拉动系统
三、实现准时化生产的条件
1、看板拉动如何实现
2、实施看板的前提条件
视频案例分析:波音777生产线
2、看板系统设计与使用
1、看板的种类与用途
2、看板系统设计思路
3、看板运转六大纪律
4、看板拉动系统
视频案例分享:某汽车厂拉动生产视频
现场模拟演练:折纸飞机
第九讲:问题分析与解决
一、问题概述
1、问题定义
2、问题的三种类型
3、解决问题的两大方向
二、问题解决八步法
1、明确问题
2、设定目标
3、分析原因
4、确定根因
5、确定对策
6、有效实施
7、结果评估
8、标准化与推广
案例分析:某企业题分析与解决案例
案例演练:如何制定对策
第十讲:持续改善
一、现场定位
二、现场改善
1、方向
2、三现主义
3、现场改善的基础
三、现场改善提案与QCC
1、马斯诺需求层次
2、改善提案与QQC
四、现场改善的金科玉律
总结,答疑!
精益生产运营管理系统培训解决方案
课程背景:
随着中央经济工作会议“五大关键词”和“供给侧””提质增效“一带一路”政策的进一步影响,尤其近期原材料价格不断攀升,经济市场持续恶化,大讲的制造业企业不同程度的受到了影响,那么企业将面临着有历史以来的挑战,我们企业怎么才能立足和突破呢?
动车比传统的火车跑的快三倍,主要原因是动车的每节车厢都有一个发动机,而传统的火车只有前面车头的牵引后面的推动,引申到管理理念就是“火车跑的快全凭车头带”这种理念显然是过时的口号,现代正确的理念是“发挥每节车厢的动力,全公司动起来”,而精益生产管理的全员改善正是符合这个理念。
“打铁还得自身硬”,我们是到了解决内部浪费问题的时候了,我们完全可以实现轻资产运营管理,使企业的利润持续增长。让我们专业和实战的导师和大家一起分析和学习吧!
课程时间:2天,6小时/天
课程对象:生产一线中基层管理人员
课程大纲:
第一讲:传统管理意识的转变
一、历史迫使我们转变
1.国内企业生产管理模式分析
2.国外企业生产管理模式借鉴
3.未来生产管理发展方向
引言部分:精益生产管理意识的转变
一、精益生产概论
1. 精益生产起源与原理
2. 精益、精细、精准三大概念实施场景
思考:为什么要做精益生产
工具:精益生产五大指导原则、丰田4P模型
3. 生产成本与利润的关系
4. 无缝管理与管理流程
5. 精益之屋解读
第一讲:生产现场精益先从浪费识别开始
一、生产现场八大浪费现象(如何形成的?有什么危害?)
1. (Waiting)等待的浪费
——等待:上级指令、外部回复、下级回复、生产联系
2. (Over-production)过量生产的浪费
——造成原因:工作进度不协调、信息传递不顺畅、生产计划做不到有效贯彻执行
3. (Inventory)库存闲置的浪费
——库存的浪费(原材料、生产过程、成品库存)、工序复杂的浪费、职能闲置的浪费、信息流的节流闲置浪费
4. (Correction)不良作业及无序浪费
——质量控制不到位的浪费、不遵守流程作业的浪费
5. (Conveyance)搬运及失职的浪费
——多余动作的浪费、工作任务完成不到位的浪费、布局不合理的浪费、虎头蛇尾的浪费
6. (Mistake)失误及低效的浪费
——工作无质量浪费
7. 动作的浪费
——现场布局不合理、十二种典型的动作浪费现象
8. 管理成本的浪费
——计划编制无依据混乱、计划不执行、计划处置不当、成本意识不强
总结:生产现场八大浪费现象归类——现场人、机、料、法、环、信息
第二讲:精益生产现场人员管理
一、开启生产员工心理密码
1. 不同类型员工的心理状态
2. 如何利用不同员工特点开展工作
3. 前喻时代员工的特点及管理方法(60-70年代)
4. 并喻时代员工的特点及管理方法(80-90年代)
5. 后喻时代员工的特点及管理方法(00后年代)
1)兼有积极和消极的工作态度
2)多变的职业观点
3)对成功的独到界定
4)对权威的看法
5)信息化的优势
6)不太喜欢循规蹈矩
7)忠于自己的生活方式,而不是自己的工作
二、解开沟通密码
1. 现场管理沟通密码
2. 如何和不同类型的上级有效沟通
3. 如何和平级沟通
4. 如何和你下属沟通
互动:现场分析不同性格的处事规则,解读协密码
第三讲:精益现场效率提升
一、生产计划的编排
1. 同期化思考与生产计划编排
2. 生产节拍的控制
3. 生产周计划. 月计划. 日计划的编排
4. 生产计划甘特图的制作
案例:某公司的生产计划
二、现场准时化生产技术的运用
1. 现代流水线的布置
2. 生产物流的控制关键点
3. JIT技术的运用
4. 单件流技术的实施要领
三、现场快速切换技术的运用
1. 应对“多品种. 小批量”订单的秘诀
2. 快速切换技术的技术要领
3. 快速切换技术实施步骤
案例互动:一顿完美的早餐
四、现场TOC技术的运用
1. 木桶原理新解读
2. TOC技术介绍
3. TOC技术的实施要领
案例互动:爸爸的红茶
第四讲:精益生产现场环境管理(6S活动)(案例图片分析其的步骤与要领)
1. 整理
2. 整顿
3. 清扫
4. 清洁
5. 素养
6. 安全
案例分析:6S目标化推行与落实. 关键要素列举
第五讲:精益生产现场质量管理
一、质量意识的改变
1. 什么是质量
2. 质量成本有哪些
3. 品质问题没有折扣
4. 精益生产解决质量问题的办法
案例分析:海尔的质量意识
二、现场分析质量问题的方法
1. 头脑风暴法
2. 5W法
3. 4M1E法
4. 如何写质量分析报告
案例互动:如何灵活能运用所学方法做质量分析
三、质量问题的处理方法
1. 戴明的PDCA循环
2. 过程作业模式技巧
3. 生产操作标准写作技巧
4. QCC活动的实施方法
案例分析:某国内大型企业的QCC活动
四、标准化作业指导部下四步法(不完善的指导方法演练)(一个视频场景)
1. 正确的指导方法演练
方法:工作指导4阶段法
——让对方准备学习、说明作业、让对方做做看、看看教导之后
2. 正确运用阶段法的4项准备工作
——订立训练计划、分解作业(作业分解的讲解-标准案例)、准备全部的东西、整理作业场
案例互动:提高员工实际操作技能的指导要点
第六讲:精益生产现场设备管理
一、认识设备管理
1. 设备管理在生产管理中的地位
2. 设备管理中的十大浪费
3. 设备管理的衡量指标
4. 案例分析设备的衡量指标—OEE
二、开展自主保养活动
1. 如何理解自主保养
2. 班组长如何实施自主保养
3. 企业实践自主保全活动7步骤
Step1:初期清扫
Step2:污染源及困难处所对策
Step3:制定自主保养临时基准书
Step4:总点检
Step5:自主点检
Step6:工程品质标准化
Step7:彻底的自主管理
4. 成功推行自主保全的要点
演练:TPM自主保全活动计划书及活动要点讨论
三、TPM计划保全活动实务展开
1. 计划保全的基本观念体系
2. 如何正确处理计划保全与自主保全的关联
3. 设备日常维修履历管理
4. 实践设备零故障的7个步骤
Step1:使用条件差异分析
Step2:问题点对策
Step3:制定计划保养临时基准书
Step4:自然劣化对策
Step5:点检效率化
Step6:M-Q关联分析
Step7:点检预知化
分享:TPM活动企业成功案例
演练:TPM计划保全活动计划书及活动要点讨论
第七讲:精益生产现场改善常用方法(实施借鉴)
方法1:“头脑风暴法”
方法2:“特性要因理论”
方法3:“4M1E理论”
方法4:“柏拉图分析”
方法5:“对赌行为”(解决执行力问题实施诀窍)
案例分析:某大型企业现场质量改善各种工具灵活运用
使用人群
- 骨干员工,管理者
课程亮点
- 专业指导
免费领取试听名额
名额有限 领完为止
相关推荐
通知:本页信息由注册会员(机构)自行发布或提供,所有内容仅供参考,最终以机构的官方信息为准,任何关于对机构的推荐都不能替代您的考察核实,本站不承担相关内容和推荐所引起的法律责任。如果您的知识产权或其他合法权益被侵犯,请立即向我们发出"权利通知书",我们将根据相关法律法规采取相应的措施予以处理,切实维护您的合法权利。联系我们:18615226315@163.com